Information
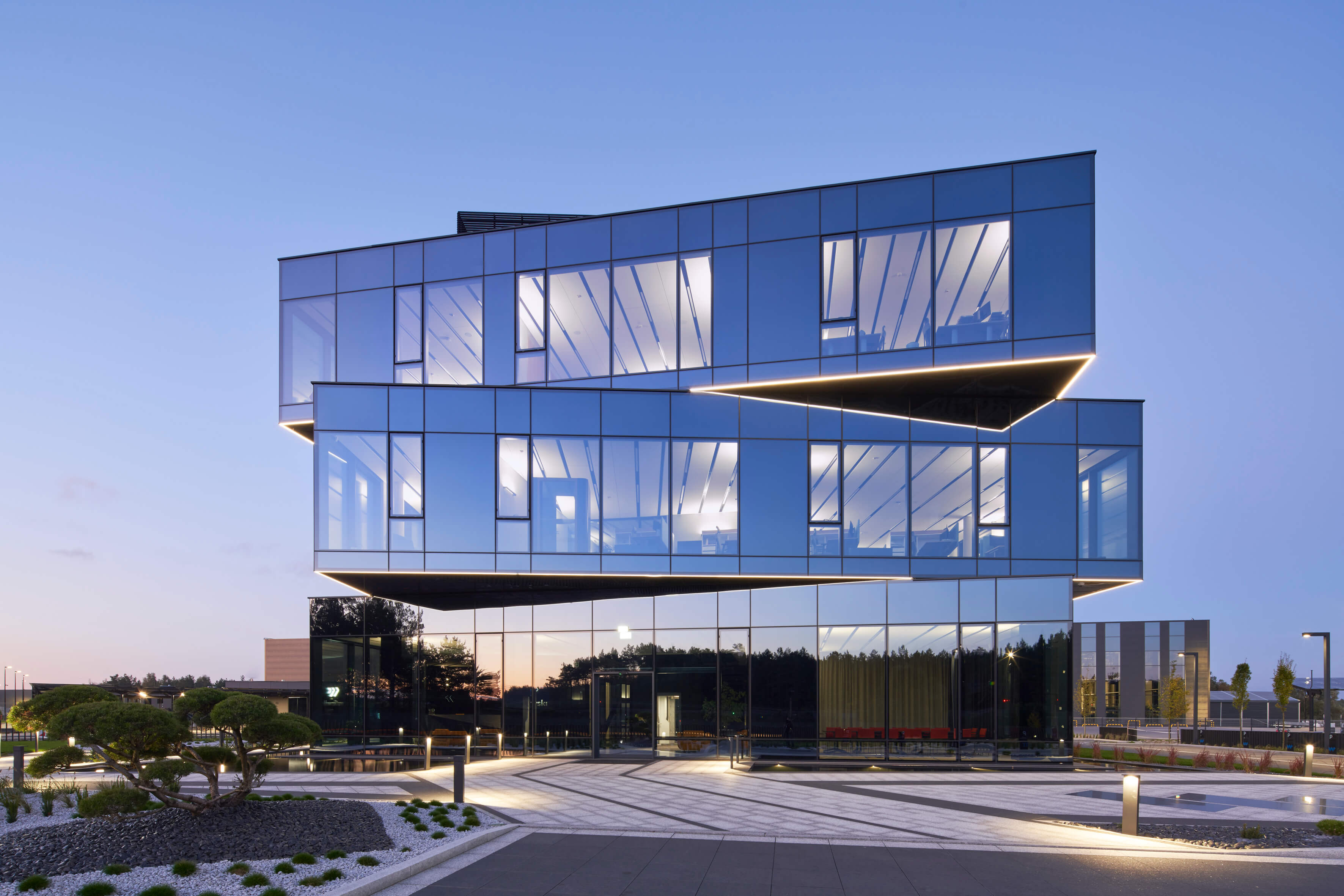
Float glass: the foundation of modern glass applications
Float glass: the foundation of modern glass applications
Float glass, the most common type of glass in modern society, is the foundation of a wide range of applications, from architectural marvels to everyday objects. Its exceptional transparency, flatness and versatility have made it the first choice material for many industries, revolutionising the way we live, work and interact with the world around us.
The genesis of float glass: a revolutionary production process
The invention of the float glass process in the 1950s marked a turning point in glass production, bringing in an era of unparalleled quality and performance. Prior to this groundbreaking invention, the large-scale production of perfectly flat and distortion-free sheets of glass posed an enormous challenge. Traditional methods, such as flat glass production, required grinding and polishing the glass sheets – a labour-intensive and costly process that limited both production capacity and affordability.
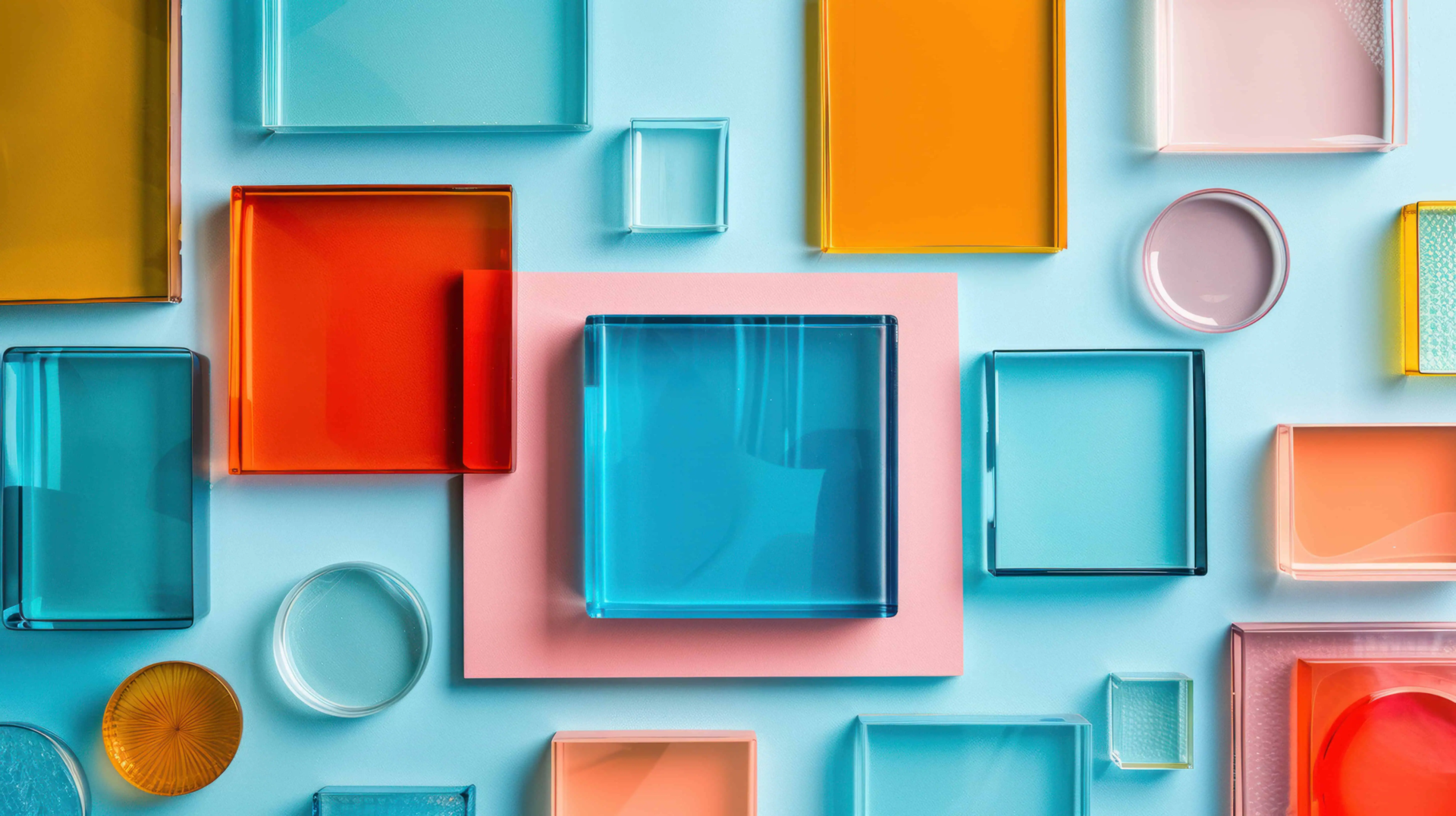
The float glass production process, pioneered by Sir Alastair Pilkington, revolutionised the industry. The process begins by melting a mixture of silica sand, sodium carbonate, limestone and dolomite in a furnace at temperatures exceeding 1,500°C. The molten glass mass, which looks like a glowing river of liquid, flows out of the furnace directly into a so-called flotation bath filled with molten tin. In The bath determines how thick the glass ribbon is to be. The glass mass spreads across it, while gravity and surface tension work together to create an extremely flat and uniform surface. Tin has a higher specific gravity than glass, which prevents it from sinking, allowing it to spread naturally and form a sheet of uniform thickness. This “floating” process eliminates the need for sanding and polishing, resulting in a much smoother and optically superior glass surface compared to previously used traditional methods.
A clean look: the characteristic properties of float glass
The most important properties of float glass are a direct result of its unique manufacturing process. The process itself already imparts the combination of desirable characteristics that have elevated float glass to the forefront of the glass industry:
● Exceptional transparency: Float glass boasts a high level of transparency, allowing light to pass through it with minimal distortion.
● Versatility and processability: Float glass can be easily processed to meet specific requirements.
The diverse applications of float glass
The versatility of float glass has led to its extensive use in many industries:
Architecture and construction:
● Windows and doors
● Facades and curtain walls
● Skylights and glazing
● Glasshouses and conservatories
Interior design and furniture:
● Mirrors
● Table tops and shelves
● Dividers and partitions
● Shower enclosures and doors
The future of float glass
Despite being a mature technology, float glass is still evolving. Key trends shaping the future of float glass production and further float glass processing include:
● Energy-efficient coatings
● Self-cleaning and anti-reflective coatings
● Smart glass technologies
● Increased strength and safety
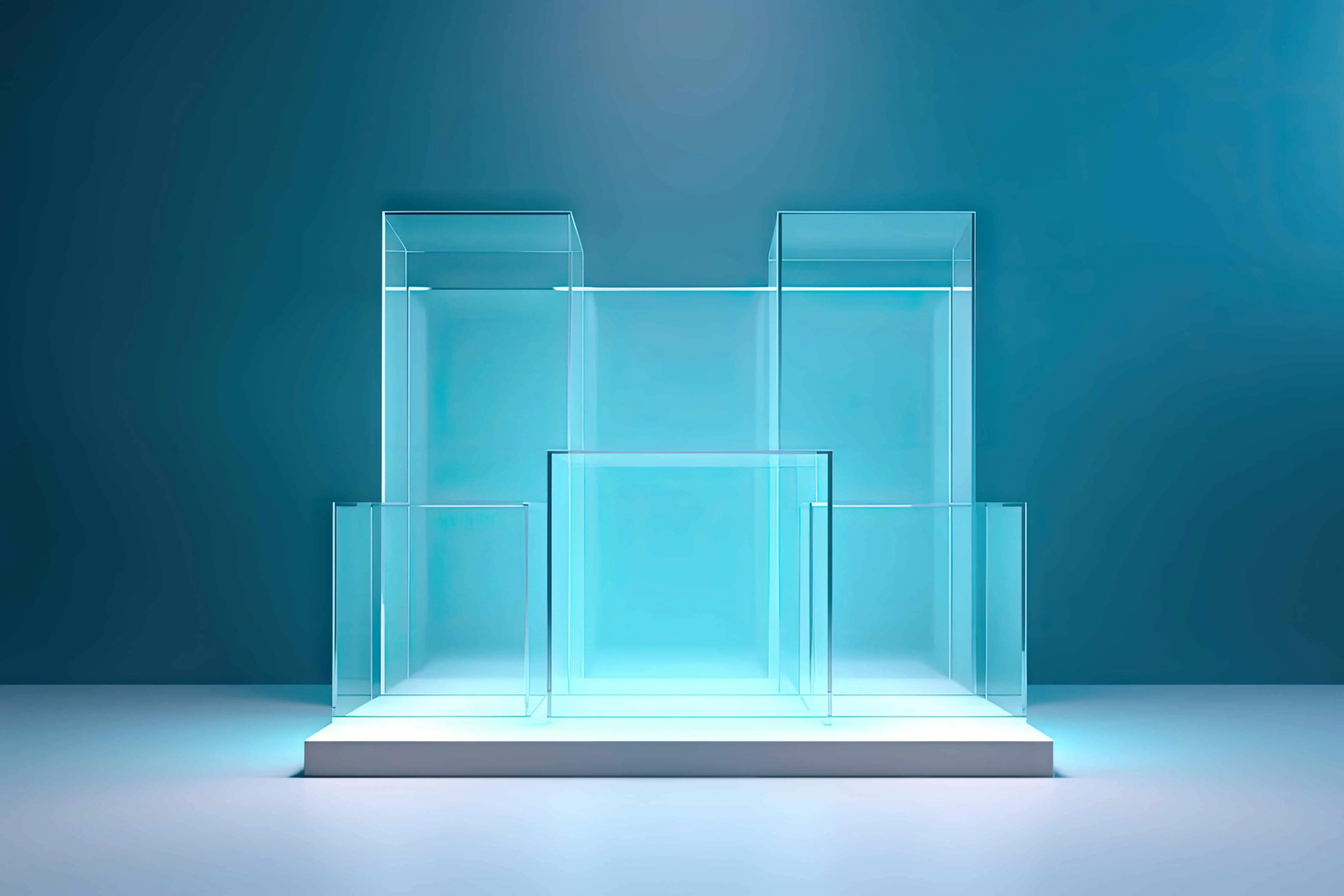
Summary
Float glass, being a testimony to human ingenuity and technological advances, has become an essential material in modern society. Its exceptional transparency, flatness, versatility, affordability and ability to be further processed, have made it possible to use it in countless applications, shaping the way we live, work and interact with the world around us.